In today's age of environmental consciousness, the packaging industry is undergoing a transformative change. As businesses grapple with the challenge of reducing their carbon footprint, molded pulp packaging emerges as a leading contender. This eco-friendly solution, crafted predominantly from water and recycled paper, offers molded fibre packaging solutions that prioritize sustainability without compromising on quality.
History and evolution of molded pulp packaging
The simplistic molded paper pulp packaging, first conceptualized in the early 20th century, has witnessed profound transformations over the decades. In its formative years, molded pulp catered primarily to the need for protecting fragile items like eggs. By the mid-century, pulp molded packaging expanded its reach to protect fruits, especially the delicate varieties. With the dawn of the new millennium, technological strides championed the cause of molded pulp. Its adaptability flourished, catering not just to food items but also venturing into sectors like electronics, medical equipment, and more. Molded pulp design guidelines from recent years show that contemporary variants are more eco-friendly, versatile, and tailored for diverse applications, showcasing the packaging industry's commitment to sustainable innovation.
What is molded pulp?
Molded pulp is birthed from a simple concoction of water and paper, typically sourced from cardboard, newspapers, or a blend of both. If you've ever wondered how to make molded pulp packaging, this is the foundation. These ingredients, when amalgamated, metamorphose into a slurry. This slurry undergoes a transformation through shaping, pressing, and drying processes to emerge as formed paper packaging—a sturdy, eco-friendly alternative to traditional packaging.
Versatility at its best
Molded paper packaging, also commonly referred to as pulp packaging, has gracefully proven its versatility by spanning its applications across several industries, including medical, produce, industrial, and horticulture. Its pliability has made it a darling for businesses looking for bespoke molded pulp packaging solutions tailored to their unique needs.
The production process
Manufacturing pulp packaging kicks off with designing the moulds that will shape the end product. These moulds, guided by molded pulp design guidelines, are integral to producing consistent and quality packaging materials. In the manufacturing facility, Wet Pressing Technology is employed, where the pulp slurry is vacuum-formed into the desired mold. Once dried, the molded pulp retains its rigid, durable shape.
Advantages of molded pulp
Molded pulp packaging offers both immediate and long-term benefits that businesses should consider when making eco-conscious choices:
- Eco-friendly stewardship: Adopting pulp molded packaging directly reduces a company's carbon footprint.
- Easy disposal: After serving its primary purpose, molded pulp can either be composted or recycled.
- Biodegradability: Molded pulp degrades naturally over time, distinguishing it from other molded paper packaging materials.
- Enhanced brand image: Companies that use molded pulp packaging can position themselves as eco-conscious businesses.
- Reduction in harmful plastics: This leads to less environmental pollution and decreased health concerns.
- Efficient shipping: Due to its lightweight design, using molded fibre packaging solutions can lead to significant shipping savings
- Expanded customer reach: As the demand for sustainable products grows, companies using molded pulp will appeal to a wider eco-conscious consumer base.
{{cta-sample-request}}
Different types of molded pulp
1. Traditional molded pulp (thick-walled):
Traditional molded pulp packaging, crafted using a single mold, features products with a robust thickness between 5mm to 10mm. Distinctively, one side is smoother while the other tends to be rough. This form of molded paper pulp packaging is perfect for supporting non-fragile, heavier items such as vehicle parts and furniture, as well as floral and nursery containers. An essential characteristic of this type is its oven-dried finish. It's most commonly utilized for egg cartons and fruit trays, offering high protection for fragile items. Its compostable and biodegradable nature further enhances its eco-friendly credentials. However, its rougher surface can sometimes be less ideal for certain product types, and some might find it lacking in aesthetic appeal.
2. Processed molded pulp:
Going beyond the simple molding and curing of pulp molded packaging, the processed variety undergoes additional treatments, which can range from pressing and die-cutting to coloring or adding embossments. This variant truly showcases the diversity of molded fiber. Its molded pulp design guidelines revolve around specialized designs, additives, and functionalities, catering to a wide array of applications. Notably, the smoother surfaces of this formed paper packaging make it suitable for electronic devices and delicate items, enhancing its visual appeal. However, this comes at the cost of a slightly more expensive production process, and these are less commonly recycled than the traditional variant.
3. Thermoformed fiber (thin-walled):
Diving deeper into how to make molded pulp packaging more refined, thermoformed fiber, manufactured using multiple heated molds, comes into the picture. These products, typically having a wall thickness of 2mm to 4mm, possess smooth, well-defined forms. Their in-mold drying process gifts them a unique finish, making them resemble thermoformed plastic products in appearance. This molded pulp packaging is highly customizable and can replace many plastic products, such as clamshell packaging. However, its more energy-intensive production process and higher costs when compared to other types can sometimes be a drawback for businesses.
4. Transfer molded pulp:
Transfer molded pulp, crafted using a dual mold process, results in products with a thickness ranging from 3mm to 5mm. Known for having smoother surfaces than the traditional method, this molded fibre packaging solution is versatile. From egg cartons and electronic packaging to hospital disposables and office equipment, its applications are vast. Just like its predecessor, this type undergoes an oven-drying process. While it's typically chosen for more upscale packaging solutions due to its refined appearance, it is slightly pricier because of the intricate production process. Moreover, in the spectrum of molded paper packaging, it might be a tad less eco-friendly than its traditional counterpart.
The impact of pulp packaging
Molded pulp packaging is leaving an impression in eco-friendly packaging, combining environmental care with flexibility. Starting in the early 20th century to protect items like eggs, it has undergone a remarkable evolution serving industries like electronics, medical, and gardening. The spectrum of molded pulp, from the traditional thick-walled to the refined transfer molded type, showcases the breadth of its application and adaptability. It offers many benefits, from reducing carbon footprints and advocating biodegradability to presenting brands as eco-conscious entities, positioning it as an optimal choice for businesses aspiring to align with today's ecological imperatives. The designs and production processes of molded pulp cater to both the aesthetic and functional needs of products, all while promoting a greener tomorrow. As we transition into an age deeply conscious of the environment, molded pulp stands out as a symbol of innovative sustainability in packaging.
Request a free sample now!
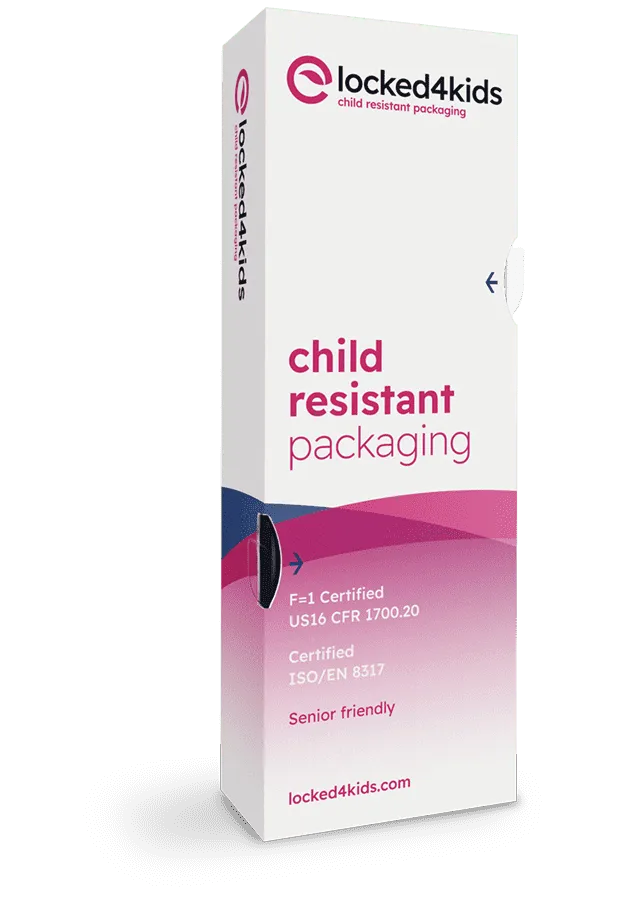